The term "form factor" is used in the computer industry to describe the shape and size of computer components, like drives, motherboards and power supplies. When hard disk drives initially made their way into microprocessor-based computers, they used magnetic platters up to 8 inches in diameter. Because that was the largest single component inside the HDD, it defined the minimum width of the HDD housing---the metal box around the guts of the drive.
This is a guest post by Kent Smith, senior director of marketing for LSI's Flash Components Division,
overseeing all outbound marketing and performance analysis for the company.
The height was dictated by the number of platters stacked on the motor (about 14 for the largest configurations). Over time the standard size of the magnetic patter diameter shrank, which allowed the HDD width to decrease as well. The computer industry used the platter diameter dimensions to describe the HDD form factors, and those contours shrank over the years. Those 8" HDDs for datacenter storage and desktop PCs shed size to 5" to today's 3.5", and laptop HDDs, starting at 2.5", are now as small as 1.8".
What defines an SSD form factor?
When solid state drives first started replacing HDDs, they had to fit into computer chassis or laptop drive bays built for HDDs, so they had to conform to HDD dimensions. The two SSDs shown below are form factor identical twins---without the outer casing---to 1.8" and 2.5" HDDs. The SSDs also use standard SATA connectors, but note that the SATA connector for 1.8" devices is narrower than the 2.5" devices to accommodate the smaller width.
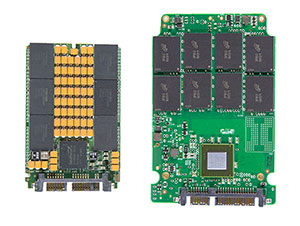
Internal circuit board of 1.8″ and 2.5″ SSD without the case
However, there's no requirement for the SSD to match the shape of a typical HDD form factor. In fact some of the early SSDs slid into the high-speed PCIe slots inside the computer chassis, not into the drive bays. A PCIe SSD card solution resembles an add-in graphic card and installs the same way in the PCIe slot since the physical interface is PCIe.
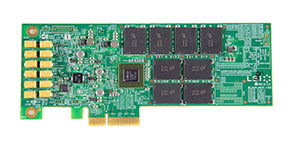
SSD manufactured as a PCIe expansion card
The largest component of an SSD is a flash memory chip so, depending on how many flash chips are used, manufacturers have virtually limitless options in defining dimensions. JEDEC (Joint Electronic Device Engineering Council) defines technical standards for the electronic industry including SSD form factors. JEDEC defined the MO-297 standard, which establishes parameters for the layout, connector locations and dimensions of 54mm x 39mm Serial ATA (SATA) SSDs, so they can use the same connector as standard 2.5" HDDs, but fit into a much smaller space.
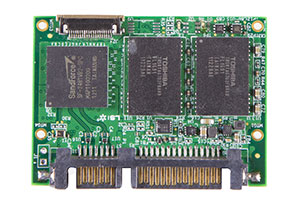
MO-297 with standard width (2.5") SATA connector
The most important element of an SSD form factor is the interface connector, the conduit to the host computer. In the early days of SSDs, that connector was typically the same SATA connector used with HDDs. But over time the width of some SSDs became smaller than the SATA connector itself, driving the need for new connectors.
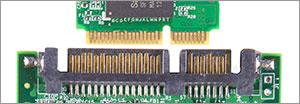
Standard SATA connector is too large for small form factors
Card edge connectors - the part of a computer board that plugs into a computer - emerged to enable smaller designs and to further reduce manufacturing and component costs by requiring the installation of only a single female socket on the host as a receptor for the edge of the SSD's printed circuit board. (The original 2.5" and 1.8" SSD SATA connector required both a male and female plastic connector to mate the SSD to the computer).
With standardization of these connectors critical to ensuring interoperability among different manufacturers, a few organizations have defined standards for these new connectors. JEDEC defined the MO-300 (50.8mm x 29.85mm), which uses a mini-SATA (mSATA) connector, the same physical connector as mini PCI Express, although the two are not electrically compatible. SSD manufacturers have used that same mSATA edge connector and board width, but customized the length to accommodate more flash chips for higher capacity SSDs.
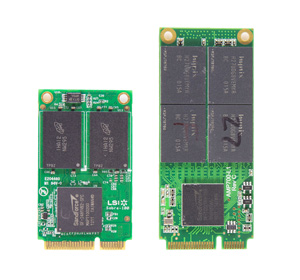
MO-300 mSATA (left) and custom-length mSATA (right)
In 2012 a new, even smaller form factor was introduced as Next Generation Form Factor (NGFF), but was later renamed to M.2. The M.2 standard defines a long list of optional board sizes, and the connector supports both SATA and PCIe electrical interfaces. The keyways or notches on the connector can help determine the interface and number of PCIe lanes possible to the board.
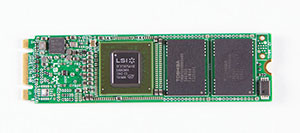
M.2 form factor supports PCIe and SATA, with many board size options
Apple's MacBook Air and some MacBook Pro systems use an SSD with a connector and dimensions that closely resemble those of the M.2 form factor. In fact, MacBooks have used a number of different connectors and interfaces for its SSD over the years. Apple used a custom connector with SATA signals from 2010 through 2012 and in 2013 switched to a custom connector with PCIe signals.
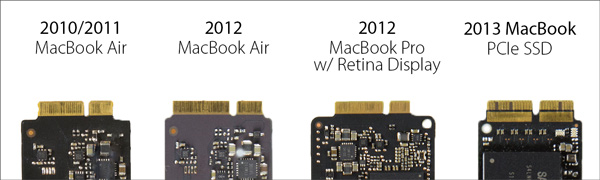
MacBook Air SSDs with custom SATA and PCIe connectors
In some cases, standard SSD form factor configurations are not an option, so SSD manufacturers have taken it upon themselves to create custom board and interface configurations that meet those less typical needs.
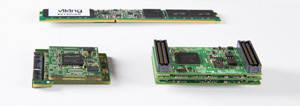
Various custom SSD form factors and connectors
And finally there's the ubiquitous USB-based connection. While USB flash drives have been around for nearly a decade, many people do not realize the performance of these devices can vary by 10 to 20 times. Typically a USB flash drive is used to make data portable---replacing the old floppy disk. In those cases the speed of the device is not critical since it is used infrequently.
Now with the high speed USB 3 interface, a SATA-to-USB 3 bridge chip, and a high performance flash controller like the LSI SandForce controller, these external devices can operate as a primary system SSDs, performing as fast as a standard SSD inside the system. The primary advantages of these SSDs are removability and transportability while providing high-speed operation.
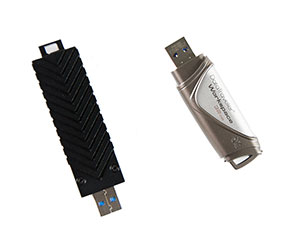
USB host interface containing high-speed SSDs
If there's one constant in life, it's demand for ever smaller storage form factors that prompt changes in circuit layout, connector position and, of course, dimensions. New connectors proposed for future generations of storage devices like the SFF-8639 specification will enable multiple interfaces and data path channels on the same connector. A similar connector - like SFF-8639, very large and built to support multiple data paths - is the SATA Express connector.
Without a spinning platter inside a box, designers can let their imaginations run wild. Creative people in the industry will continue to find new applications for SSDs that were previously restricted by the internal components of HDDs. That creativity and flexibility will take on growing importance as we continue to press datacenters and consumer electronics to do more with less, reminding us that size does in fact matter.
Masthead image credit: SSDs and keyboard image via Shutterstock